What are cobots?
Cobots, the robots that will revolutionise your daily routine
Business Collaborative work AI
Robots and humans can work together like colleagues thanks to the boom in collaborative robots. The use of cobots in industry is changing production processes because unlike industrial robots, they work efficiently, safely and skilfully with other employees on all types of tasks.
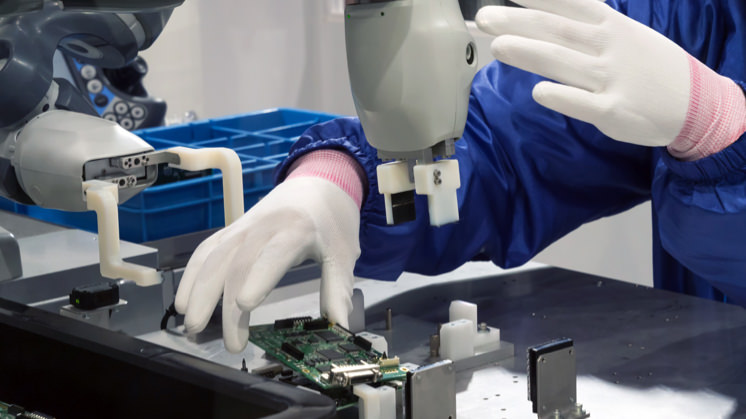
Cobots share jobs with operators, collaborating, manoeuvring and interacting with them. They are not intended to replace humans, rather to become their bodyguards. These machines release operators from dangerous, repetitive and burdensome tasks, reducing absence due to illness and occupational illnesses. They also have sensors that detect human presence and react, for example by slowing down to protect humans from injury. These lightweight devices — some of which weigh less than 10 kilos — are easy to transport to any point in the production chain.
The boom in collaborative robots
Collaborative robots, known by the abbreviation cobots, are nothing new. They first appeared at the end of the 1990s as the result of a research project, but now, almost a quarter of a century later, they are finding their way into companies, large and small, to transform the productive model and play a role in the great 4.0 Industrial Revolution.
Cobots are a technological marvel. They have artificial vision to detect and interact with workers and accessories that enable them to perform numerous tasks. The main ones are polishing, laboratory tests, machine supervision, injection moulding, packaging, quality control, assembly, bolting, adhesion, welding, etc. If we want a robot to collaborate with a person, it needs to learn with the person and be able to change its behaviour. That's where Artificial Intelligence (AI) and Machine Learning come in.
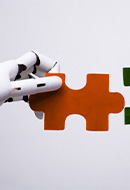
Robotisation of work
Robots will do many of the jobs that humans now do.
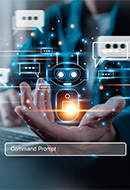
What is Artificial Intelligence?
AI is set to bring about a revolution on a par with the Internet.
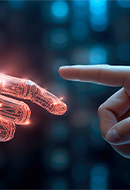
History of artificial intelligence
Get to know the almost century-old set of conceptions behind artificial intelligence.
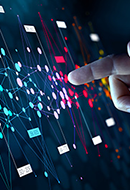
AI Algorithms
Get an insight into the diversity of algorithms that make up AI.
What makes robots different to cobots
Cobots, as we have seen, are used to perform high precision tasks which are tiring for human operators, leading to mistakes. This frees humans up to focus on added value tasks to offer clients better services. This is just one of the many benefits of using collaborative rather than traditional robots:
The strong points of cobots
SEE INFOGRAPHIC: The strong points of cobots [PDF]
External link, opens in new window.
The growth of cobots
Cobots are the fastest growing segment in industrial automation. The collaborative robot market is expected to grow by 20% per year until 2028, according to the report Collaborative Robot Market – 2024 by Interact Analysis. Daniel Frisch, sales manager at Universal Robots, one of the main manufacturers, says that cobots are increasingly affordable and are drastically reducing the automation barrier, reaching areas hitherto considered complex or costly.
The International Robotics Federation (IRF) The International Federation of Robotics (IFR) estimates that the installation of robots will grow exponentially. The market demands more and more products tailored to meet customer requirements. This is where cobots become great allies, since one of their main virtues is that they can manufacture short series of numerous parts.